总体而言,不规则形状的或内部放置了嵌入件的中空结构的HP-RTM(高压树脂传递模塑成型)复合材料部件,其外面可以是一层碳纤维增强复合材料(CFRP),内部则是一个可导出的金属芯材。
这项技术的专利还在申请之中,与此同时,已经可以以此进行工业化生产了。
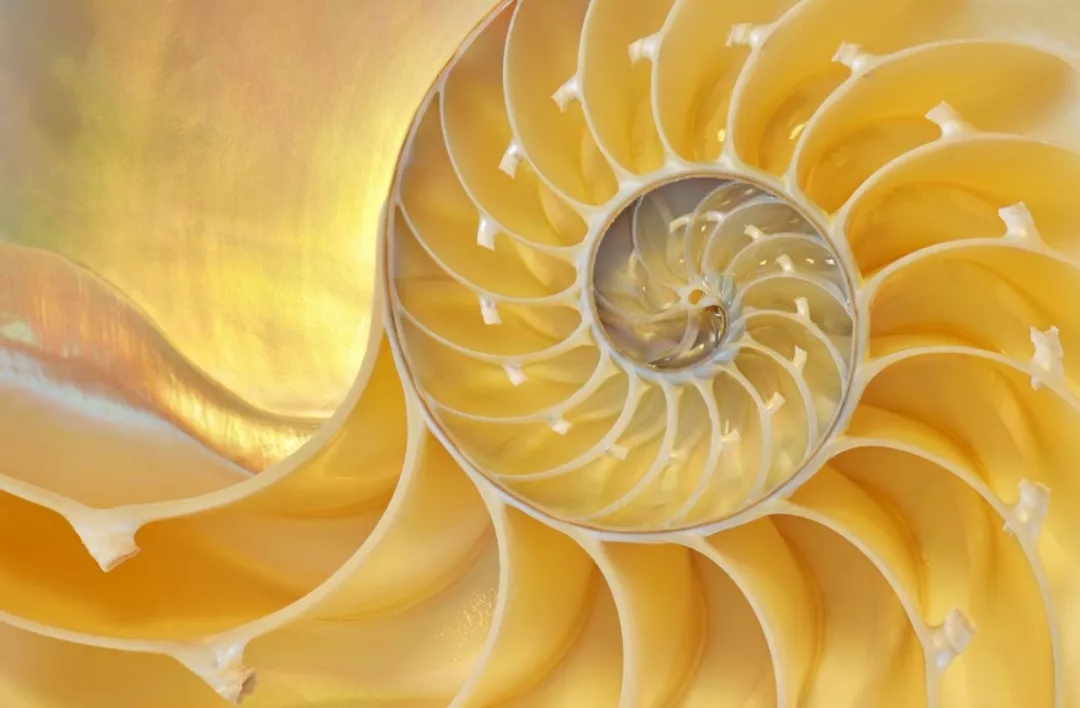
历史的发展
近年来,碳纤维复合材料的浸润工艺发展很快,这是因为宝马公司需要以一种高效且重复性好的方式生产数以万计的复合材料部件,并以此制造出非常轻的电动汽车,以满足大城市的人们乘车出行的需要。
宝马公司及其复合材料部件供应商因此投入巨额资金,开发高压树脂传递模塑成型(HP-RTM)工艺。
这项工艺是用高压将树脂注入模具内,来对纤维进行浸润。
可快速固化成型的聚氨酯或环氧树脂原料,先经过精确计量,再通过一个装在模具上的混合头进行高压混合。
如此,模具的型腔即是模塑成型部件的外形。所以,通常是生产有一定形状的三维片状结构的部件,而不是那种类似中空结构的部件,因为如果要使部件外形趋向中空的形状,纤维很容易产生皱褶。
树脂充满模具型腔并浸润模腔内的碳纤维片材,这里的碳纤维片材可以是几层碳纤维织物叠放在一起的片材,模具的合模吨位有几千吨(400~4000t)。
从闭合的模具内抽出所有的空气,在模腔和纤维织物叠材内都形成真空。
然后,树脂经高压混合头注入模具型腔内,再在纤维织物的纹理间流动直至完全浸润所有的纤维片材。
为避免最终的产品中有气泡,会适量多注一点树脂,以使其从模具的接缝处流出来。
树脂会从混合头的注入口进入模内,克服流动阻力,逐渐充满模腔,直至完全浸润纤维织物的纹理。
树脂在模腔内扩散时,可监测树脂在注入口附近的压力逐渐升高到一定的值,以前树脂在充满模腔时,这个压力的峰值通常是80~100 bar,最近一些 客户已经用到的压力峰值为130bar,所以他们会要求压力峰值到200bar。
最终的压力值总是会更高,原因之一是树脂的反应时间一直在缩短,现在每100s(以前是每5~6min)就能提取一件产品。
其二是压力峰值更高,模塑件的树脂可以更紧实,因此复合材料中树脂的量已经达到40%~45%左右。这个树脂比例已经可与用热压罐加工预浸料生产的航空复合材料部件的树脂比例相媲美了。
需解决的问题
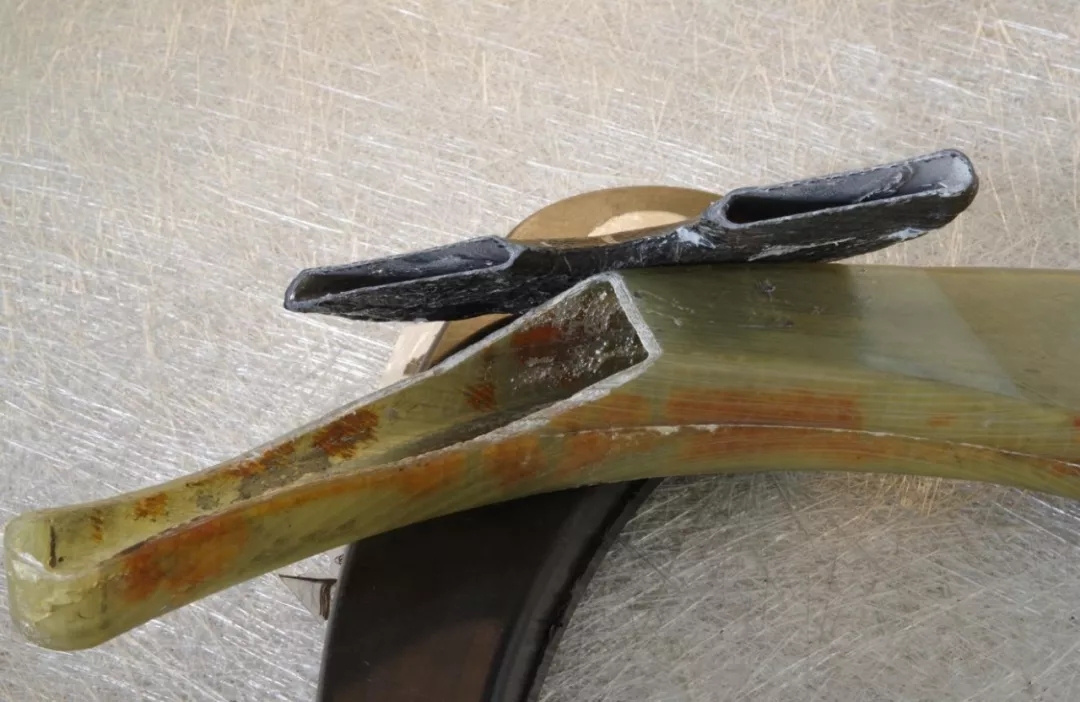
因此,为了能用高压树脂传递模塑成型(HP-RTM)工艺生产高品质的碳纤维增强复合材料(CFRP)结构件,必须要在碳纤维叠材的表面施加至少80bar的单位压力。
如果是一个片状结构的碳纤维叠材,可以用一个足够吨位的压机压紧模具的上下模,以保证达到碳纤维叠材表面需要的压力。
然而,如果要生产中空结构的部件,则需要增强它的结构强度同时又不增加太多重量,一种方法是先做出一个部件的两半,然后再粘合在一起;另一种 方法是在中空的位置放一个轻质芯材或一个可导出的重的芯材用于承压,以避免把中空的部件压扁。
轻质芯材(为轻木或泡沫)不能被导出来,承压也不能超过15~20bars。
或者可以用一种硬的多孔砾岩做可导出的芯材,最终部件模塑成型后,砾岩可在水中分解并溶解。
分解后的砾岩粉末,可以通过在碳纤维复合材料的表面钻的小孔排出来。但即使是这种“砾岩”,承压也不能超过30bars。
还有一种办法是用那种软的充满了液体的承压袋,用以抵抗液体树脂的压力(液体承压袋是脆性的,还容易变形,体积不能大,否则不便于取出)。
厚的液体承压袋会以要求的峰值压力做预加压,但可能会因为太重而没办法从模塑的部件中取出,或是很难从不规则的中空内腔里取出,而且液体承压袋也难以去到空腔内狭小的边角。
康隆(Cannon)Afros的解决方案
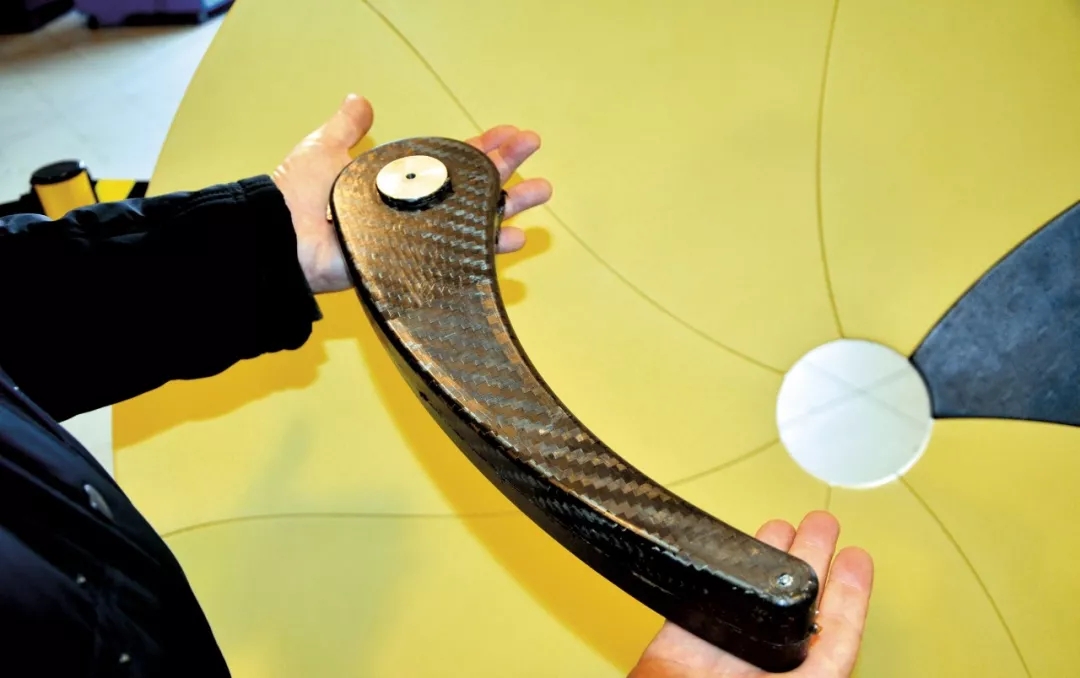
采用一个金属芯材,其外形可与最终的碳纤维增强复合材料(CFRP)中空结构件的内腔形状完全一致,最终碳纤部件制作完成后,再导出金属芯材。
这种芯材还便于容纳金属嵌入件或在铸造中嵌入定位销。
可以用一种低共熔点的合金制造这种金属芯材,其熔点温度也低于一般碳纤维增强复合材料(CFRP)结构树脂所能承受的温度(通常固化温度大约在130~ 140℃,能承受再高30℃的温度而不损伤最终部件)。
已经发现有几种金属合金的熔点是从略高于室温开始,直到250℃。
将金属合金倒入一个模具中,模具内可预先固定上嵌入件。
为避免气泡、收缩和粘连等问题,模具会预先加热到接近共熔合金的熔点温度。在模内涂上一层脱模粉,模具有开孔并带有提取销和密封垫,可避免出 现过多的毛边或金属熔液浪费。
金属芯材一成型,即马上脱模、去毛边并清除脱模粉,检查嵌入件的位置正确,同时确保芯材的表面和内部没有气泡。
先依次在高压树脂传递模塑成型(HP-RTM)的模具内正确地铺上几层纤维片材,再把芯材放进HP-RTM的模具内,然后用纤维叠材包裹好芯材。
需要注意的是,纤维是有导向的(放置方向正确,可以让部件有更好的支撑),纤维叠材需进行预成型,使其成为适合放进模具的形状。
芯材压在下面的纤维叠材上,上面也铺有纤维叠材。然后,HP-RTM的模具合模,此时检查模具的真空密封性,加压推入树脂浸润纤维的外表面。
先将模具预热至树脂固化温度(大约130℃),再高压注入树脂,需要至少一个传感器在模腔注入口附近以监测扩散压力,也可以在外围的几个点上加装 传感器来监测扩散压力,还可以加装一些电容式传感器以探测树脂是否已流到部件的边角或薄的位置,确保树脂充满整个模腔。
一旦达到需要的峰值压力(210 bar),混合头关闭,进入再循环模式。等固化时间结束后,压机打开再取出部件。
之后,有两种生产方式可供选择:
第一种生产方式是再加热,把部件放入一个模板护架内,再送进加热炉内,通过辐射或感应将芯材和空气加热至共熔合金的熔化温度。熔化的低共熔 合金通过预先钻的小孔从模板护架内排出来,形成中空式复合材料部件的内部空腔,嵌入件会留在需要的位置,使其成为碳纤维增强复合材料(CFRP)的一部分。
第二种生产方式是将部件冷却,让金属芯材留在部件内,金属芯材在后面的机械加工过程中可起到增强结构的作用。硬的金属芯材更利于整个部件的放置以及对部件进行切割和去毛边的操作,因为在机加工时,金属芯材可降低振动并避免部件变形。待机加工完成后,经检查合格的部件,再将其放入一个模板护架内,送进加热炉内熔化低共熔合金芯材,使其能够从小孔中完全排出来。
此外,低共熔合金的熔化温度(135~220℃)低,必要的话可使部件旋转,即可排空所有的低共熔合金,即使部件边角位置的低共熔合金液体也可以完全排出来。
而如果空腔是用承压袋或其他材料填充的,则承压的材料可能无法到达边角位置,或无法完全排出。
熔化的低共熔合金液体排出后,可以使其流进热熔炉下面的一个储存罐中进行回收,最后倒回低共熔合金的坩埚中以循环使用。
还可以用这项技术生产大型部件的空腔芯材,以替代原来的多孔砾岩芯材。虽然多孔砾岩的失蜡法模塑工艺可以抵抗很高的温度,但其抗压性能差(多孔砾岩最后可通过振动破碎或水溶法被排出)。
总之,中空结构的碳纤维增强复合材料(CFRP)部件可以用于很多领域,像机械手的运动部件、传动机构、形状不规则的结构件、非圆柱形的罐体以及液体和压缩气体的储罐等。